Industries
most of the industries covered
Each industry has its specificities and types of processes. Fives ProSim offers a full range of software to support engineers in their decision-making, engineering studies and the operation of their processes.
Whatever industry you are interested in, modeling and simulation is a great way to understand and improve your processes to meet the growing demands for efficiency, safety and the environment.
Fives ProSim has customers in practically all the process industries:
- chemicals and petrochemicals: ammonia and fertilizer plants, olefins, ethylene crackers, polymers, fine and specialty chemicals, inorganic chemicals, solvent regeneration, etc.
- gas and oil production: off-shore platforms, on-shore fields, LNG plants and terminals, gas dehydration, desulfurization, gas treatment, pipelines…
- refining: atmospheric and vacuum distillations, isomerization, catalytic reforming, hydro-treatment, hydro-desulfurization, alkylation, FCC, visbreaking, etc.
- energy: combined cycles / cogeneration, nuclear energy, coal treatment, gasification, water and utilities…
- … and many other areas: alcohols, air separation, carbon capture and storage, bio-fuels, pharmaceuticals, ingredients, flavors and fragrance, pulp and paper, food industry, metallurgy…
Fives ProSim and the energy transition
With an increased focus on climate change and energy transition, companies are moving to more sustainable operations. In this context, Fives ProSim develops the tools that allow industries to reduce their carbon footprint, to be more energy efficient and to make the best use of available resources (raw materials, water…).
Today most of the companies see CO2 reduction as a competitive advantage. But in order to achieve this reduction, they need to quantify the impact of the modifications to the plants they can imagine on their CO2 footprint as well as the corresponding costs (both CAPEX and OPEX). The software we offer are essential tools to tackle decarbonization challenges: design appropriate carbon capture units, develop new technologies in this field, perform sensitivity analysis, optimize operating parameters, generate the data necessary for an LCA analysis, find ways to use captured CO2 as raw material to synthetize other molecules…
Hydrogen is also a huge initiative area where Fives ProSim technology is required to design and operate production plant, to optimize distribution network, to test new concepts in order to produce green hydrogen with models before moving forward…
Everyone knows that the greenest energy is the one that is no longer consumed. Improving energy efficiency of industrial processes is no longer an option. Fives ProSim brings to the market software tools allowing to reduce energy consumption: process energy balances, exergy analysis, pinch technology for both energy and water consumption reductions, etc.
Having accurate thermodynamic models and being able to simulate all the equipment of a processing plant and optimizing their operation are key.
Fives ProSim is today at the heart of the challenges that the industry must meet to remain competitive.
You would like to learn more about our activities?
Process simulation software Engineering services About us Contact us
Major industrial challenges addressed
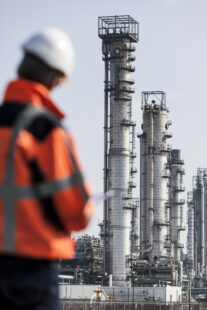
We guide you to efficiency
The use of simulation to design, develop, fine-tune or improve the operation of manufacturing processes has considerable advantages.
This makes it possible to easily and rigorously establish the material and energy balances on a complete process or a simple unit operation. The economic evaluation of CAPEX and OPEX as well as of the environmental impact calculation complete this analysis.
Compared to a more empirical or experimental approach, the modeling approach is:
- Less costly: allows to carry out “virtual” experiments instead of “real” experiments in lab or on pilot plants which are often expensive in raw materials, staff … when exploring different ways and analyzing the influence of several parameters.
- Very fast: it becomes possible to easily assess different process configurations, different operating conditions.
- Safe: critical scenarios (very reactive chemical substances, high pressure and / or temperatures, etc.), emergency stops… can be studied, without risk for the equipment nor the personnel.
- Innovative: one can easily explore unconventional technologies instead of reproducing on the industrial unit what is done in the lab.
Beyond these economic and operational advantages, the simulation approach allows a deeper understanding of the production process and the sustainability of this knowledge acquired in the form of a process model.
Simulation makes it possible to face, or even anticipate, a changing economic environment. Process modification studies can be done quickly (sensitivity analyzes) to meet new regulations (safety, environment). The impacts linked to new raw materials or to a different quality of products can be quickly estimated and the consequences in terms of investment evaluated.